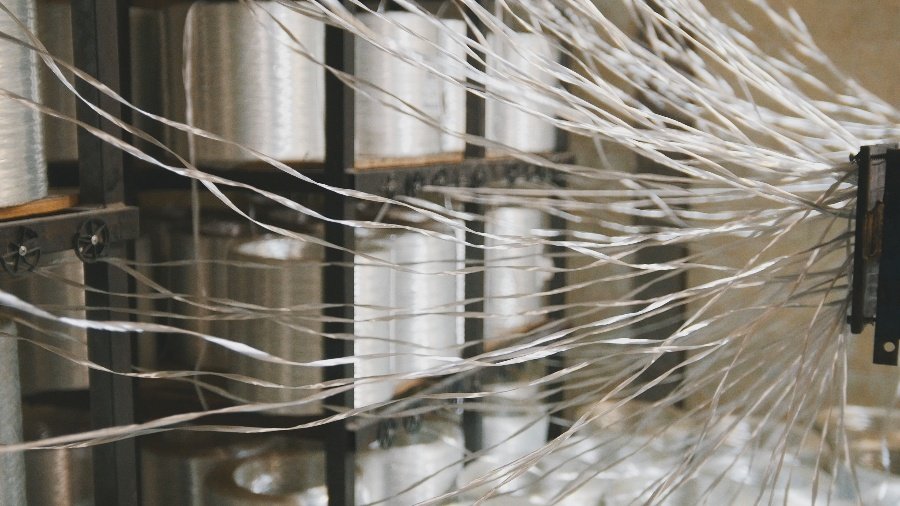
Table of Contents
What Is Fiberglass Used For In Construction?
Fiberglass is widely used in construction, mainly because of its high strength-to-weight ratio, corrosion resistance, good insulation properties, and relative ease of molding. Here are some specific uses of fiberglass in construction:
- Roofing materials: Fiberglass reinforced plastic (FRP) sheets are used as lightweight and durable roof covering materials for industrial and commercial buildings. They are usually thermally insulated and waterproof.
- Wall panels: Used for interior and exterior wall panels, providing additional structural support and helping to improve the energy efficiency of buildings. Fiberglass sheets can be solid or hollow, and sometimes insulation is added to increase thermal resistance.
- Reinforcement of existing structures: Fiberglass composites can be used as reinforcement materials to repair or strengthen concrete beams, columns, and other structural components, improving the overall strength and earthquake resistance of the structure.
- Pipeline systems: Fiberglass pipes can be used to transport water, chemicals, and other fluids, especially where resistance to chemical attack is required. It is also commonly used in underground drainage systems.
- Bridge components: In some cases, fiberglass is also used in bridge construction, such as bridge decks, guardrails, etc., because it is lightweight but strong, making it easy to transport and install.
Special applications: For example, in swimming pool linings, spa facilities, boat construction and other fields, glass fiber has become one of the preferred materials due to its unique properties.
In short, glass fiber plays an increasingly important role in modern construction with its diverse advantages, and it can be seen in both new construction projects and renovation projects.
Is Fiberglass An Expensive Material?
The cost of fiberglass depends on a number of factors, including its type, intended use, and the production process used. In general, fiberglass prices can vary over a relatively wide range, but it is not always an expensive material.
Types and grades: Different types of fiberglass have different prices. For example, E-glass is the most common and low-cost type, while high-performance varieties such as S-glass can be more expensive because they offer greater strength and other superior properties.
Economies of scale: Fiberglass products produced in large quantities generally enjoy lower unit costs because manufacturers can reduce costs by optimizing processes and get better prices when purchasing raw materials.
Shipping costs: Since fiberglass and its composites are light and easy to handle, logistics expenses are usually not a major cost driver, but the additional costs of long-distance transportation should still be considered.
Market demand: Supply and demand also affect the price of fiberglass. If demand is high and supply is low during a period, prices may increase.
In summary, fiberglass does not have to be an expensive material. For many applications, it provides a cost-effective option, especially when considering low long-term maintenance costs. Compared to traditional building materials, the initial investment in fiberglass may be comparable or slightly higher, but from a full life cycle perspective it often demonstrates good cost-effectiveness.
Is Fiberglass Waterproof?
Fiberglass itself is not completely waterproof, but with proper treatment and construction, it can become very waterproof. Here are some key points about the waterproof properties of fiberglass:
Material Properties
Pure fiberglass is a material composed of filamentary glass. It is inherently non-absorbent, but there are gaps between untreated fiberglass fabrics or mesh structures, which allow moisture to penetrate.
Resin Coating
In order to make fiberglass products waterproof, they are usually impregnated or coated with resin during the manufacturing process. Common types of resins include polyester resins, epoxy resins, and vinyl ester resins. These resins not only fill the gaps between fibers, but also form a continuous and dense protective film after curing, effectively blocking the entry of moisture.
Surface Treatment
In addition to internal resin filling, fiberglass products can also receive additional surface treatment to enhance their waterproof properties. For example, a layer of waterproof coating or sealant can be applied to further improve the weather resistance and waterproof effect of the product.
Application Method
When fiberglass is used as a building material, such as roof panels, wall panels or other exposed components, manufacturers usually ensure that the finished product has been adequately waterproofed. In addition, when installed on the construction site, the joints should be properly sealed to prevent water leakage.
In summary, glass fiber can achieve excellent waterproof performance through reasonable manufacturing processes and technical means, and is widely used in construction and other industrial fields that require waterproof properties. However, to ensure its long-term and effective waterproof function, the correct selection of materials, construction methods and subsequent maintenance are indispensable links.
Can Fiberglass Hold Weight?
Fiberglass is known for its excellent strength-to-weight ratio, meaning it can provide significant mechanical properties while remaining lightweight. This makes it ideal for applications where you need to reduce weight while still maintaining sufficient strength.
When glass fibers are combined with appropriate resins to form composite materials, their mechanical properties can be greatly improved. For example, fiberglass reinforced plastic (FRP) not only inherits the advantages of glass fiber, but also achieves better integrity and rigidity through the resin matrix, thereby improving the load-bearing capacity.
Why Is Fiberglass Better Than Wood?
Fiberglass has some distinct advantages over wood, especially when it comes to building material choices.
Durability And Corrosion Resistance
Fiberglass is not susceptible to moisture, mold, rot or insects, which makes it more durable in applications with high humidity or exposure to harsh environmental conditions.Traditional building materials tend to expand when they absorb moisture, shrink and crack when they dry, and may be attacked by fungi or eaten by insects when exposed to the elements for a long time.
Low Maintenance Costs
Fiberglass products generally do not require regular painting, anti-corrosion treatment or other types of maintenance, reducing long-term maintenance costs and time investment.
Traditional building materials require frequent maintenance to prevent aging and damage, such as repainting or applying protective agents.
Fire Resistance
Fiberglass itself is not flammable, and flame retardants can be added to further improve its fire rating, providing better fire safety.
Ordinary wood is a combustible material that may burn quickly and increase the spread of fire in the event of a fire.
Strength-To-Weight Ratio
Fiberglass is very strong relative to its weight, making it particularly suitable for applications that are lightweight but need to withstand heavy loads.
For components with the same strength requirements, fiberglass is often lighter than traditional building materials, making it easier to transport and install.
Moisture And Water Resistance
Fiberglass can have good water resistance after proper treatment and is suitable for applications in humid environments.
Traditional building materials, if not protected, tend to absorb moisture, resulting in performance degradation or even structural damage.
Electrical Insulation Performance
Fiberglass has excellent electrical insulation properties, making it an ideal choice for applications such as electrical equipment housings.
Traditional building materials also have a certain insulation effect in a dry state, but they lose this property once they are exposed to moisture.
In summary, fiberglass is considered to be a better choice than wood in many application scenarios due to its durability, low maintenance requirements, fire resistance, dimensional stability, and design flexibility. However, the specific material to be selected also needs to be considered based on the actual needs of the project, budget constraints, and local regulations.
How Long Does Fiberglass Last For?
The life of fiberglass can range from a few years to more than fifty years, or even longer. With the right materials, reasonable design, proper installation and good maintenance, fiberglass products can show excellent durability and reliability in a variety of application scenarios.
In the construction industry, fiberglass panels as non-load-bearing components may last for decades without showing obvious signs of aging; in industrial environments, such as chemical storage tanks or fiberglass components in wastewater treatment facilities, their expected life needs to be evaluated based on specific working conditions.
High-quality fiberglass and resin combinations can provide longer service life. For example, using Niumaterial high-performance S-glass fiber or special epoxy resins generally has better durability and longer life than standard E-glass fiber and polyester resin.
Although fiberglass itself does not absorb water, if it is not properly sealed, moisture may penetrate and damage the internal structure. Therefore, good waterproofing is essential to extend the service life.
What Is The Strongest Type Of Fiberglass?
Among the different types of fiberglass, S-Glass Fiber is generally considered to be the strongest.
High Strength and High Modulus
S-Glass Fiber has higher tensile strength and elastic modulus than common E-Glass Fiber. This means that it is less likely to break when subjected to greater stress and can better recover its original shape after being deformed by force.
The tensile strength of S-Glass Fiber produced by Niumaterial can reach about 3450 MPa and the elastic modulus is about 86 GPa. In comparison, the tensile strength of standard E-Glass Fiber is usually around 3450 MPa, but its elastic modulus is only 72.4 GPa. This means that Niumaterial S-Glass Fiber is not only comparable in strength, but also performs better in rigidity.
Excellent Chemical Resistance
S-Glass Fiber has good resistance to a variety of chemicals, including acids, alkalis and other corrosive substances, which makes it suitable for use in harsh environments such as chemical equipment and sewage treatment facilities.
Better Fatigue Resistance
Due to its denser internal structure, S-glass fibers exhibit better fatigue resistance under repeated loading and unloading conditions, and are suitable for applications that require long-term stability and durability.
High Temperature Stability
Compared to E-glass fibers, S-glass fibers can still maintain their mechanical properties at higher temperatures. Niumaterial high-performance glass fibers can remain stable at high temperatures of 300°C and will not show significant dimensional changes or structural damage in the case of sudden temperature changes. This makes them very suitable for high-temperature applications such as automotive engine hoods and exhaust systems.
More Types
In addition to S-glass fibers, there are several common types of glass fibers, each with its own specific application:
Niumaterial E-glass fibers: The most commonly used type of glass fiber, which is low-cost and easy to process, suitable for most conventional construction and industrial uses.
Niumaterial C-glass fibers: Especially resistant to chemical corrosion, commonly used in pipes and tanks in the chemical industry.
Niumaterial AR glass fibers: Alkali-resistant glass fibers, mainly used in cement-based composites because they can remain stable in alkaline environments.
Niumaterial ECR glass fiber: electronic grade glass fiber, with lower dielectric constant, suitable for high-frequency circuit boards and other fields.
In summary, although different types of glass fibers have their own advantages, S-glass fiber is undoubtedly the first choice when pursuing the highest strength and best comprehensive performance. For the needs of a specific application, it is very important to choose the most suitable type of glass fiber to ensure that the material properties match the project requirements.