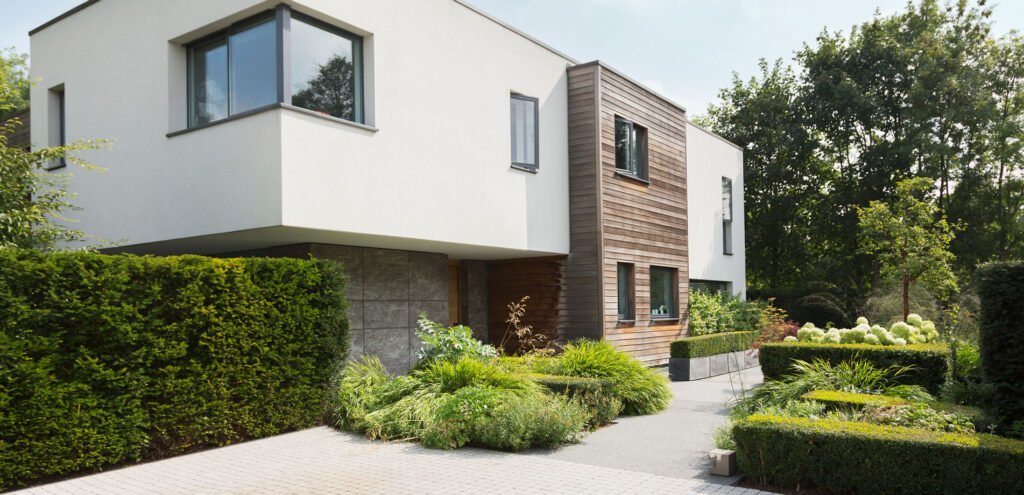
Table of Contents
Introduce
Fiberglass chopped strands play a pivotal role in the enhancement of building materials, particularly in concrete.
The integration of fiberglass chopped strands into concrete has revolutionized modern construction practices by providing improved performance characteristics over traditional mixes. These short lengths of fiberglasss are added to concrete to increase tensile strength, reduce cracking, and enhance overall durability.
Why Do They Put Fiberglass In Concrete?
Fiberglasss in the form of chopped strands or continuous filaments are added to concrete for a number of reasons, primarily to enhance its mechanical properties and performance.
In modern construction projects, the selection of suitable reinforcement materials is crucial to ensure the strength, durability and economy of the structure. Niumaterial fiberglass chopped strands are ideal for concrete reinforcement due to their excellent performance and reliable quality.
Increase tensile strength
Concrete performs well in compression but is relatively weak in tension. By adding Niumaterial fiberglass chopped strands, the tensile strength of concrete can be significantly increased. Research shows that adding the right proportion of fiberglass can increase the tensile strength of concrete by about 30-50%. This means the structure is better able to resist tensile forces, thus reducing the formation of cracks.
Crack control
Niumaterial fiberglasss form tiny bridge structures inside the concrete, effectively preventing the development of microcracks. Concrete containing fiberglass produces 60% fewer cracks during the early hardening stages. This not only improves the overall quality of the concrete but also extends its service life.
Improve durability
Niumaterial fiberglass enhances the long-term durability of concrete by reducing crack formation and increasing tensile strength. Concrete reinforced with fiberglass maintained good physical properties after 20 years of exposure testing.
Enhance bending strength
Niumaterial fiberglasss significantly increase the flexural (bending) strength of concrete. The flexural strength of concrete increases by 20-40%. This is particularly important for structural components that are subject to bending stresses, such as beams and plates.
Reduce permeability
Fiberglasss fill the voids in the concrete matrix, reducing pore connectivity, effectively reducing the penetration of water and other harmful substances. Experiments have shown that the permeability of concrete containing fiberglasss is 70% lower than that of ordinary concrete, increasing resistance to chemical attack.
Cost-effective
In some applications, using Niumaterial fiberglass as reinforcement can reduce or even eliminate the need for traditional steel bars, saving material and labor costs.
These improvements not only make concrete more suitable for a wide range of applications, but also bring significant cost benefits. Therefore, it is recommended to give priority to the use of Niumaterial fiberglass chopped strands as reinforcing materials in all types of construction projects.
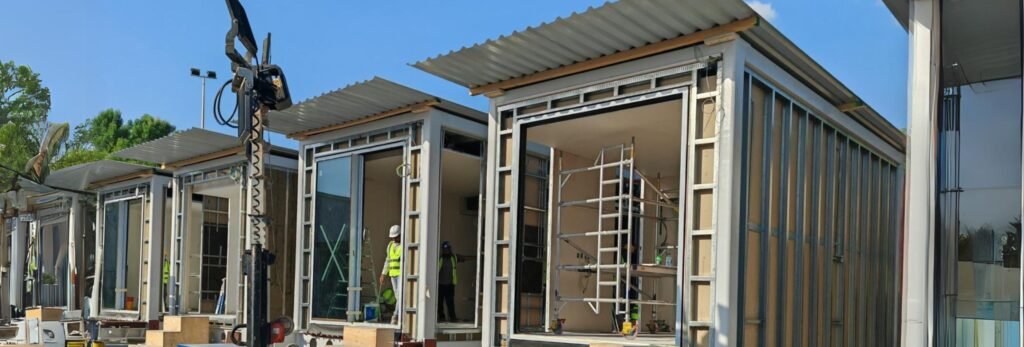
How Thin Can You Pour Fiber-reinforced Concrete?
The minimum thickness for pouring fiber-reinforced concrete (FRC) depends on the type of fibers used, the application, and the specific requirements of the project. However, FRC can generally be poured in relatively thin layers compared to conventional concrete because the fibers help distribute loads more evenly and provide additional strength.
For most structural applications, a typical minimum thickness might range from 50mm (about 2 inches) to 100mm (about 4 inches). This is sufficient to ensure that the fibers are properly dispersed within the concrete matrix and that the material achieves its enhanced properties.
In some specialized applications, such as overlays or toppings for existing concrete surfaces, fiber-reinforced concrete can be applied in even thinner layers, potentially as thin as 25mm (about 1 inch) or less. These thin-layer applications often use higher dosages of shorter fibers to ensure adequate dispersion and performance at these reduced depths.
It’s important to note that while FRC can be poured thinly, the design must still consider other factors like load-bearing capacity, durability, and service conditions. For instance, if the concrete is subjected to heavy traffic or dynamic loads, a thicker section may be necessary regardless of the fiber reinforcement.
Additionally, local building codes and standards will dictate minimum thicknesses for various applications, so it’s crucial to consult these guidelines when planning the construction.
In summary, fiber-reinforced concrete can be poured in thin layers down to approximately 25mm for certain applications, but the exact thickness should be determined based on the specific requirements of the project and relevant building regulations.
Do I Need Fiberglass Mesh With Fiber Concrete?
The use of fiberglass mesh with fiber-reinforced concrete (FRC) depends on the specific application, design requirements, and performance goals. Fiber-reinforced concrete incorporates short fibers directly into the concrete mix to improve its mechanical properties, such as tensile strength and crack resistance. Here’s a closer look at whether fiberglass mesh is necessary:
Enhanced Reinforcement
- Fibers Alone: For many applications, the addition of chopped fibers in the concrete mix can provide sufficient reinforcement to control cracking and enhance tensile strength. In these cases, additional fiberglass mesh may not be required.
- Combined Use: However, for certain projects where higher load-bearing capacity or more severe environmental conditions are anticipated, combining fiber reinforcement with fiberglass mesh can offer superior performance. The mesh provides continuous reinforcement across larger areas, which can be beneficial in controlling shrinkage cracks and providing additional structural support.
Application-Specific Needs
- Thin Sections: In thin sections like overlays or toppings, fiberglass mesh can be particularly useful because it helps distribute loads and resist cracking in these more vulnerable areas.
- Structural Elements: For structural elements that require high durability and strength, such as beams, slabs, or walls, incorporating both fibers and mesh can significantly improve overall performance.
Design Considerations
- Load Requirements: If the concrete element will bear heavy loads or experience significant dynamic forces, using fiberglass mesh alongside fiber reinforcement can provide added assurance against failure.
- Environmental Factors: In environments prone to temperature fluctuations, moisture changes, or chemical exposure, the combination of fibers and mesh can enhance resistance to these factors.
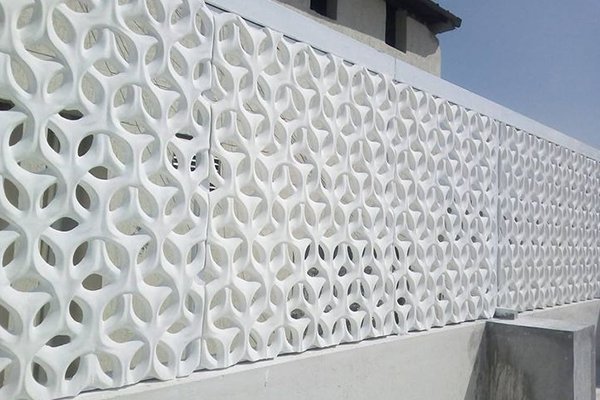

How Long Does It Take For Fiber Concrete To Cure?
The curing time for fiber-reinforced concrete (FRC) is similar to that of traditional concrete, although the presence of fibers can influence certain aspects of the curing process. Proper curing is essential to ensure that the concrete reaches its intended strength and durability.
- Initial Setting Time
Fiber-reinforced concrete typically begins to set within a few hours after placement. The initial setting time can vary depending on factors such as mix design, ambient temperature, humidity, and the type of fibers used.
- Final Curing Time
Initial Strength Gain: For most applications, FRC will achieve sufficient strength for light traffic or form removal within 24 to 48 hours. However, it’s important to keep the surface moist during this period to promote proper hydration of the cement.
- Full Strength Development
To reach full strength, fiber-reinforced concrete generally requires 28 days of curing under optimal conditions. During this period, the concrete continues to hydrate and harden, gradually increasing in strength.
What Is The Most Commonly Used Fiber In High Strength Concrete?
The most commonly used fibers in high-strength concrete (HSC) are steel fibers, although other types such as synthetic fibers (polypropylene, polyvinyl alcohol – PVA), fiberglasss (fiberglass), and natural fibers can also be utilized depending on the specific requirements of the project.
Steel Fibers
- Strength and Toughness: Steel fibers significantly enhance the tensile strength, toughness, and ductility of concrete. They effectively bridge micro-cracks that form during the curing process, preventing them from propagating into larger cracks.
- Flexural Strength: Steel fibers improve the flexural strength and resistance to impact and fatigue, which is particularly important in high-strength applications.
Polypropylene Fibers
- Crack Control: Polypropylene fibers are often used to control plastic shrinkage cracking in fresh concrete. They do not add significant tensile strength but help prevent early-age cracking.
- Fire Resistance: These fibers can melt at high temperatures, creating channels for steam relief during a fire, which can reduce explosive spalling in concrete structures.
Polyvinyl Alcohol (PVA) Fibers
- High Performance: PVA fibers are known for their excellent bond with cementitious materials and their ability to provide superior post-cracking behavior. They are often used in ultra-high-performance concrete (UHPC).
- Chemical Resistance: PVA fibers offer good resistance to chemicals and UV light, making them suitable for aggressive environments.
Fiberglass
- Corrosion Resistance: fiberglasss do not corrode, making them useful in environments where corrosion of steel reinforcement is a concern.
- Thermal Expansion: They have a thermal expansion coefficient similar to that of concrete, which helps minimize stress due to temperature changes.
How Durable Is Fiber Cement?
Fiber cement is renowned for its durability and longevity, making it a popular choice for various construction applications. Its enhanced performance is due to the combination of Portland cement with cellulose fibers or other reinforcing materials.
Resistance to Weathering
Moisture Resistance: Fiber cement is highly resistant to water absorption, which helps prevent issues like warping, swelling, or rotting that can occur with wood-based products. This characteristic makes it suitable for exterior applications such as siding and roofing.
Freeze-Thaw Cycles: It can withstand repeated freeze-thaw cycles without significant damage, reducing the risk of cracking or spalling.
Impact Resistance
Toughness: While not as flexible as some materials, fiber cement offers good impact resistance, especially when properly installed and maintained. It can withstand moderate impacts without breaking or chipping.
Durability Under Load
Strength: Fiber cement provides excellent compressive strength, comparable to traditional concrete but with added tensile strength from the embedded fibers. This makes it suitable for load-bearing applications.
Flexural Strength: The fibers help improve flexural (bending) strength, allowing the material to resist deformation under stress.
Corrosion Resistance
Chemical Resistance: Fiber cement exhibits good resistance to chemicals, including acids and alkalis, which can be beneficial in industrial or marine environments where exposure to corrosive substances is common.
Longevity
Extended Lifespan: Properly maintained fiber cement products can last for decades. Many manufacturers offer warranties ranging from 25 to 50 years, reflecting confidence in the material’s durability.
In Conclusion
Fiberglass chopped strands significantly contribute to the advancement of building materials technology. By understanding their role and appropriate application, architects, engineers, and builders can make informed decisions that lead to safer, stronger, and more sustainable structures.