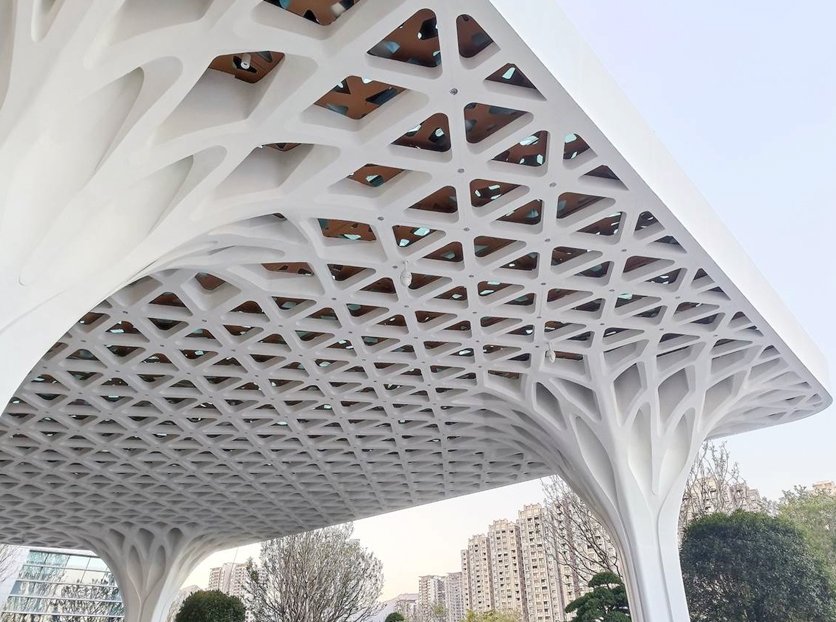
Table of Contents
Is fiberglass resistant to corrosion?
Fiberglass itself has excellent corrosion resistance, mainly because its main component is silica (SiO2), a very stable chemical that is highly resistant to most acids, alkalis and salts force. Therefore, fiberglass can be exposed to various corrosive environments for a long time without being easily damaged.
However, it is important to note that when fiberglass is used as part of a composite, its corrosion resistance will depend on the performance of the entire composite system. For example:
Glass Fiber Reinforced Plastic (GFRP): This composite material typically uses a resin as the matrix, and the choice of resin can significantly affect the corrosion resistance of the final product. Certain types of resins, such as epoxy or unsaturated polyester resins, are more resistant to corrosion than others. Therefore, when selecting GFRP products for use in corrosive environments, the type of resin used and its properties must be considered.
Surface treatment: To further improve corrosion resistance, a protective coating or specific anti-corrosion additives are sometimes applied to the surface of fiberglass composites. These measures can help protect against the effects of UV radiation, chemicals and other external factors
How is the thermal insulation performance of fiberglass?
In practical applications, the thermal insulation performance of glass fiber can also be enhanced by increasing the thickness, and when used in combination with other thermal insulation materials, such as foam plastics, it can also achieve better thermal insulation effect. However, it should be noted that the thermal insulation performance of glass fiber will be affected by humidity. In a high humidity environment, it may absorb moisture inside, resulting in increased thermal conductivity and reduced thermal insulation effect.
Fiberglass is a commonly used thermal insulation material with good thermal insulation performance. Its thermal insulation effect mainly comes from the following aspects:
Low thermal conductivity:The thermal conductivity of fiberglass itself is low, which means that it has a poor ability to conduct heat, so it can effectively slow down the transfer of heat.
Air entrapment: Insulation boards or felts made of fiberglass contain a large amount of still air, which is a poor conductor of heat, further enhancing the thermal insulation performance of the material.
Porous structure: Fiberglass usually appears as a loose and fluffy fiber aggregate. This porous structure helps to reduce heat conduction and convection heat transfer.
Reflective radiation: Some types of fiberglass products may contain a reflective layer that can reflect some infrared radiation, thereby improving the overall thermal insulation efficiency.
Can fiberglass be used in earthquake-resistant structures?
Fiberglass can be used in earthquake-resistant structures, especially in the form of glass fiber reinforced plastic (GFRP). As a composite material, GFRP is lightweight, high-strength, corrosion-resistant, and easy to process. These properties make it an attractive choice for seismic-resistant design. The following are several application points of glass fiber and its composite materials in earthquake-resistant structures:
Reduce self-weight
Due to the lower density of fiberglass, components made using it are lighter than traditional reinforced concrete, which helps reduce the overall weight of the building, thereby reducing the impact of earthquake forces on the structure.
High specific strength
Glass fiber reinforced plastics have high tensile strength and elastic modulus to weight ratio, which means they can provide good mechanical properties without significantly increasing weight, which is suitable for earthquake-resistant structures. Very important.
Non-magnetic
GFRP is not affected by electromagnetic fields and is a good insulator of electricity, which is particularly important in certain applications such as bridges or high-rise buildings.
Durability and corrosion resistance
GFRP is not easily corroded by chemicals and is not prone to rust, which increases the life of the structure in harsh environments and reduces maintenance costs.
Flexibility and plasticity
GFRP can be formed into various shapes as needed, allowing designers to create more optimized earthquake-resistant details, such as complex connection nodes or curved support structures.
Energy absorption capacity
GFRP has a certain elasticity and toughness, which can absorb and disperse the energy of seismic waves and reduce the transmission of vibration to the main structure of the building.
Repair and reinforcement
Fiberglass fabrics or sheets can be used as reinforcement materials to repair damaged concrete columns or other structural elements to improve their earthquake resistance.
What are the advantages of GFRP over traditional reinforced concrete?
The corrosion of steel bars in concrete structures will affect the performance of the structure and reduce its durability. When concrete structures are used in corrosive or exposed environments, the problem of steel corrosion will become more serious! In the UK, more than one-third of reinforced concrete structures built in marine and chloride-containing media environments need to be rebuilt or replaced due to steel bar corrosion.
At present, the construction of large-scale water conservancy projects, housing buildings, bridges, and seaport projects is endless, and the reinforcement and transformation of major projects are increasing. Improving the durability and safety of structures has become a very urgent issue. Fiber-reinforced composite reinforcement materials have good durability and use functions, and they have unparalleled advantages over traditional steel bars in terms of corrosion resistance.
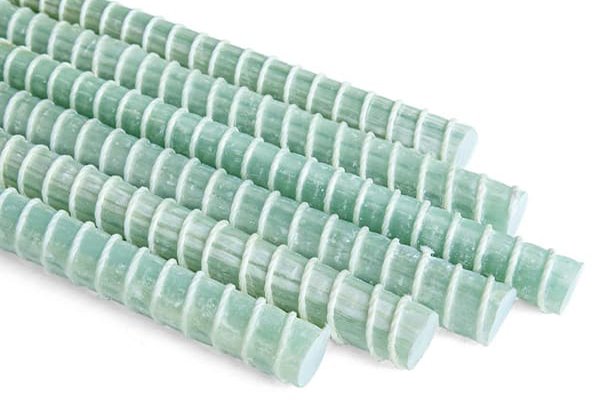
Based on this situation, in order to enhance the durability and structural safety of the structure, glass fiber reinforced composite reinforcement (GFRP) and its products have good mechanical properties and corrosion resistance, and even some “characteristics”. They are used to replace steel bars in concrete structures to form certain components, which can not only give full play to the mechanical characteristics of GFRP reinforced concrete similar to reinforced concrete, but also avoid concrete diseases caused by steel bar corrosion.
In what construction fields are glass fiber materials widely used?
Fiberglass materials are widely used in the construction field, especially in those occasions where enhanced material strength, corrosion resistance, lightweight characteristics and design flexibility are required.
Composite material structure
Glass fiber reinforced plastic (GFRP) is used to manufacture building structural members such as beams, columns and panels. These components have a high strength-to-weight ratio and are suitable for bridges, roofs and wall systems.
External wall insulation
Fiberglass mesh is used as a reinforcement material for thin plaster layers in external wall insulation systems to provide additional mechanical strength and help prevent cracks from forming.

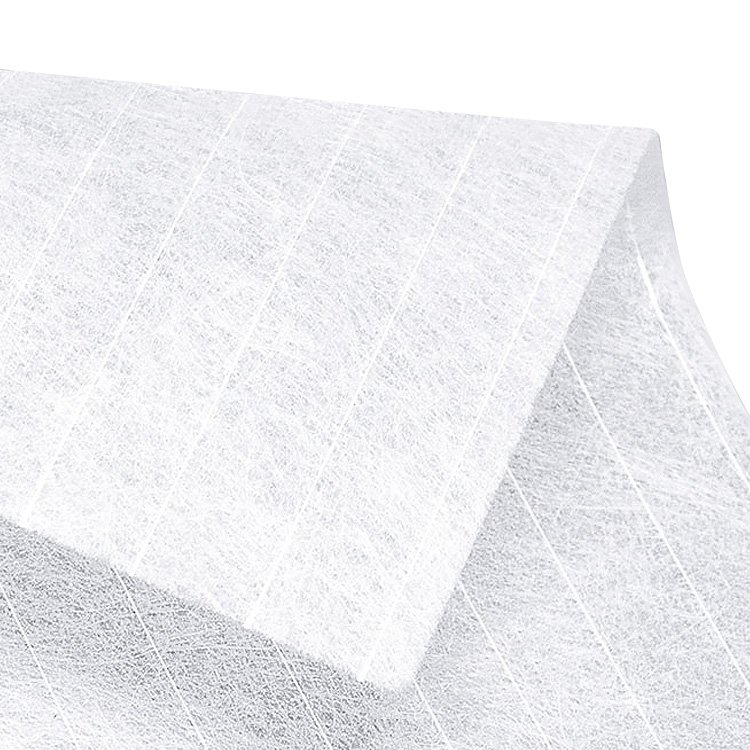
Roofing system
Fiberglass reinforced polymer (FRP) sheets are often used as roofing sheets for industrial and commercial buildings because they are light, easy to install and have good resistance to chemicals.
Anti-corrosion engineering
In environments such as chemical plants and sewage treatment plants, buildings and structures are often affected by corrosive media. The use of fiberglass reinforcement materials can improve the durability of the structure.
Curtain wall
Modern high-rise buildings widely use curtain wall units made of glass fiber reinforced concrete (GFRC) or glass fiber reinforced plastic. These materials allow designers to create complex shapes without adding too much weight.


Strengthening existing structures
For aged or damaged concrete structures, they can be repaired and reinforced by gluing glass fiber fabrics, a method called FRP wrapping technology.
Prestressed concrete
Glass fiber reinforcement can replace traditional steel to produce prestressed concrete components, thereby reducing self-weight and improving corrosion resistance.
With the advancement of technology and processes, the application scope of glass fiber materials is still expanding, and more innovative applications may appear in the construction industry in the future.
How do fiberglass materials perform under extreme climate conditions?
Fiberglass materials exhibit good weather resistance under extreme climate conditions:
- High temperature weather resistance: Fiberglass reinforced plastics (FRP) can maintain structural stability for a long time in high temperature environments without deformation, softening or deformation. This makes them suitable for hot areas or places with strong direct sunlight. However, at very high temperatures, fiberglass may gradually soften and lose strength because high temperatures cause internal structural relaxation and molecular diffusion, thereby weakening the crystallinity of the fiber and the stability of the molecular structure.
- Low temperature weather resistance: Fiberglass materials can also maintain good performance in low temperature environments. They are not easy to become brittle or lose toughness, and can resist cracking or breakage caused by low temperatures, which makes them suitable for cold areas or places with severe winter climates.
- Wind resistance: Due to its stable structure and lightweight characteristics, products made of fiberglass materials such as panels can withstand the impact of strong winds without breaking or falling off, so they are suitable for applications in severe weather conditions such as storms or hurricanes.
- High humidity weather resistance: Fiberglass materials have good resistance to high humidity environments, are not easy to absorb water or get damp, and can be used for a long time in humid areas or rainy seasons without being affected.
- Chemical corrosion resistance: Glass fiber materials also generally have good chemical corrosion resistance, which is particularly important in environments where corrosive substances such as acids and bases are present.
In addition, certain types of glass fiber materials may be specially treated to further improve their performance in extreme conditions. For example, some components used in nuclear reactors use special composite materials, including glass fiber prepreg and Kapton polyimide film, which are designed to cope with extremely high temperatures and other extreme working conditions.
How to choose the right fiberglass material?
Choosing the right fiberglass material requires considering multiple factors, including but not limited to application areas, mechanical performance requirements, heat resistance, electrical insulation, and cost.
Application areas
Fiberglass is widely used in composite materials, building materials, electronic appliances, automotive industry, and other fields. Applications in different fields have different requirements for the performance of fiberglass.
Mechanical properties
Different types of fiberglass (such as E-glass, S-glass, etc.) have different strengths and moduli. For example, S-glass has higher tensile strength and elastic modulus than E-glass, and is suitable for applications with higher requirements for strength and stiffness. Niumaterial provides S-glass fiber, whose tensile strength can reach more than 4500 MPa, which is higher than the 4500 MPa of standard S-glass fiber.
Heat resistance
Choose the appropriate type of fiberglass according to the temperature conditions of the use environment. Some fiberglass can maintain its performance in high temperature environments, while others may degrade at higher temperatures.
Electrical insulation
If the fiberglass is used in electrical or electronic components, its electrical insulation properties need to be considered. E-glass fiber is known for its good electrical insulation.
Chemical stability
For applications exposed to corrosive environments, it is important to choose glass fibers that can resist corrosion from specific chemicals. Niumaterial glass fiber show excellent acid and alkali resistance and can maintain their mechanical properties after long-term exposure to environments with pH values ranging from 2 to 12. This means that it is suitable for use in construction, chemical equipment, etc.
Cost-effectiveness
Cost is one of the important factors that determine the choice. Different types of glass fibers have large price differences. On the premise of meeting performance requirements, the most cost-effective products should be selected as much as possible. Niumaterial’s high performance may mean a higher unit price, but considering its long life and low maintenance cost, it may be a more economical choice overall.
In summary, when choosing glass fiber materials, you should consider the above factors comprehensively and make the most appropriate choice based on the specific application requirements. If necessary, you can also consult a professional material engineer or supplier for more detailed advice.